Details of Physical Properties
High temperature stiffness
AURUM™ has a high Tg (245℃)
➡Better temperature stiffness at 150℃ and higher than PEEK.
AURUM™ is thermoplastic resin
➡Can be fiber reinforced to improve initial strength.(modulus of elasticity 3 > 22 GPa ).
[Usage Applications]
thrust washers, seal rings, bearings
IC trays,
*Tg = glass transition temperature
Coefficient of expansion
AURUM™ is thermoplastic,
➡Can be filled with additives to control its coefficient of expansion.
AURUM™ has a highTg (245℃)
➡Stable coefficient of expansion at up to 245℃
[Usage Applications]
thrust washers, seal rings, turbo seals, bearings, pistons, oil pumps,
Oil seals for construction machinery,
IC trays
*Tg = glass transition temperature
Thermoplastic
AURUM™ is thermoplastic polyimide
➡Can be injection molded and unnecessary for cutting machining.
AURUM™ has 100℃ higher Tg (245℃) than PEEK
➡Better heat resistance and dimensional stability than PEEK
[Usage Applications]
thrust washers, seal rings, , bearings, pistons, oil pumps,
Oil seals for construction machinery,
IC trays,
*Tg = glass transition temperature
Sliding properties
AURUM™ has the highest critical PV value of any thermoplastic resin.
(in a non lubricated / oil lubricated condition sliding)
[Usage Applications]
thrust washers, seal rings, , bearings, oil pumps, pistons,
Outgas properties
AURUM™ has lower outgas properties at high temperature ranges than PEEK and non thermoplastic PI
[Usage Applications]
IC trays, liquid phase panel manufacturing tools,
Radiation resistance
AURUM™ exhibits better radiation resistance than PEEK and non thermoplastic PI (reduction in tensile strength is minimal)
[Usage Applications]
switches and socket components related to nuclear power,
Creep resistance
AURUM™ has a higher Tg (245℃) than PEEK
➡Superior creep resistance even at a high temp.
[Usage Applications]
Oil seals for construction machinery,
*Tg = glass transition temperature
Chemical resistance
AURUM™ has a polyimide backbone structure.
➡Excellent chemical resistance against gasoline,various lubricants, aviation fuels and cleaning agents.
[Usage Applications]
thrust washers, seal rings, turbo seals, oil pumps, pistons,
Oil seals for construction machinery,
Dialysis machine impellers,
Aircraft engine components,
Dimensional stability(shrinkage rate)
AURUM™ has half the shrinkage factor of PEEK (AURUM™:0.7%, PEEK:1.5-2.0%), and produces superior dimensionalaccuracy in fiber reinforced grade products.
Its dimensional accuracy make post molding process unnecessary for molded products that requires high dimensional accuracy.
[Usage Applications]
thrust washers, seal rings, oil pumps, pistons, valve seats,
Oil seals for construction machinery,
IC trays,
High Voltage durability
AURUM™ can maintain low dielectric constant even at high temperatures and exhibits excellent insulation properties under high-temperature conditions.
Dielectric constant at 240℃: AURUM™: 2.5, PEEK: 3.6
Due to its excellent insulation properties at high temperatures, it allows for the thinning of the insulation film even in high-voltage environments that generate high heat, contributing to the improvement of the packing density of magnet wires.
[Usage Applications]
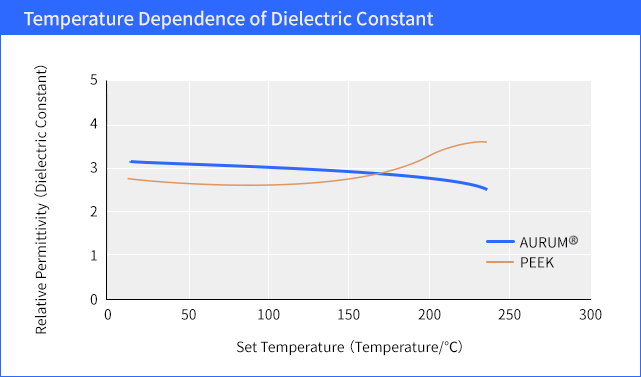
Thrust washers for transmissions: sliding properties and reduced weight
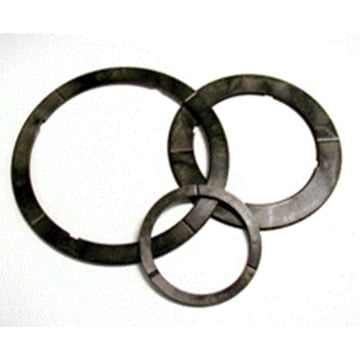
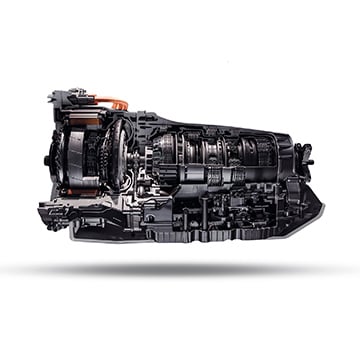
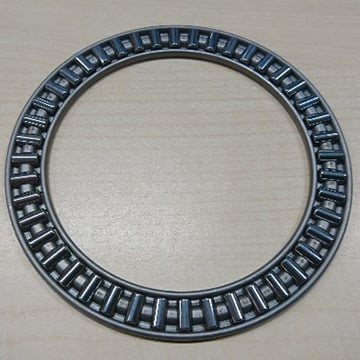
Conventional materials
Metal (steel), PEEK, non-thermoplastic PI
Issues
Compared with metals: reduced weight, sliding properties (self-lubricating), damage to other components in the event of breakage
Required Properties
Compared with resins: critical PV value (high temperature stiffness), dimensional accuracy
Advantages with AURUM™
- Low weight
- Reduced damage to other components
- High PV rating
- Dimensional accuracy
Effects of weight reduction: approx. 60% (compared with SUS)
Can be used in sliding applications with harsh environments (use for large-diameter washers)
Recommended grades
Seal rings for transmissions: sliding properties, dimensional accuracy
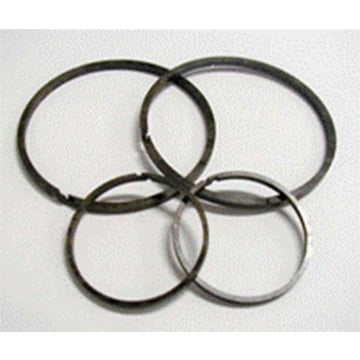
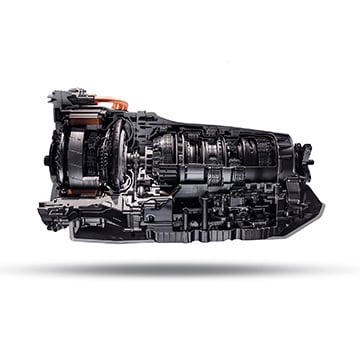
Conventional materials
PEEK, non-thermoplastic PI
Issues
PEEK: critical PV value, dimensional stability at 150℃ and higher (Gap control)
Non-thermoplastic PI: Gap joint shape flexibility, dimensional stability
Required Properties
Sliding properties (critical PV value), coefficient of expansion, chemical resistance (ATF properties)
Advantages with AURUM™
- High PV rating
- Dimensional accuracy
- Gap joint shape flexibility
Can be used in sliding applications with harsh environments (in environments of 150℃ and higher)
Gap joint shape flexibility (thermoplastic resin)
Recommended grades
Turbo charger abradable seal: improved sealing properties
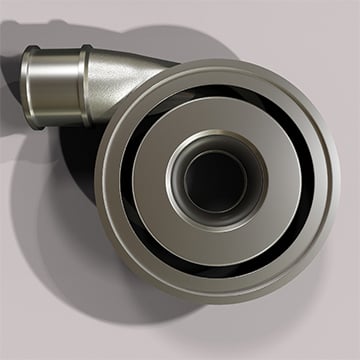
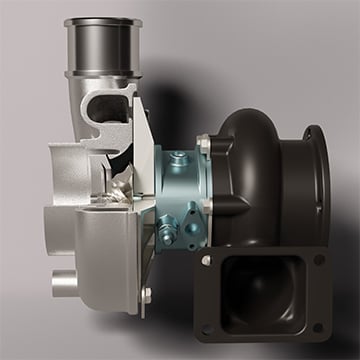
Conventional materials
Metal (AI), PI coating, PTFE material
Issues
Metals: gap control (limited due to metal-to-metal contact)
Resins: coefficient of expansion (-60 - 230℃), high cost due to cutting
Required Properties
Coefficient of expansion, low damage to other materials, chemical resistance (blow-by resistance)
Advantages with AURUM™
- Coefficient of expansion
- Reduced damage to other components
- Injection molding (low cost)
Reduced fuel consumption: 2% reduction
Recommended grades
Bearings: high sliding properties, creep resistance
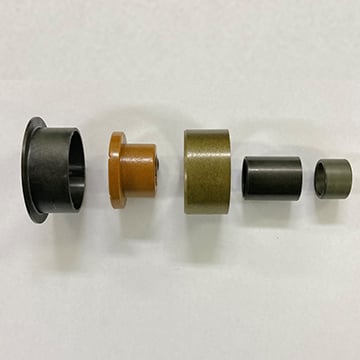
Conventional materials
Metal, against thermoplastic resin
Issues
Metals: self lubrication
Resins: critical PV value, creep resistance
Required Properties
Molded products with high dimensional accuracy due to injection molding
Advantages with AURUM™
- Critical PV value (high temperatures)
- Creep resistance
- Self lubrication (against metals)
Can be applied to bearings in harsh environments (around 245℃)
Recommended grades
Pistons: reduced weight
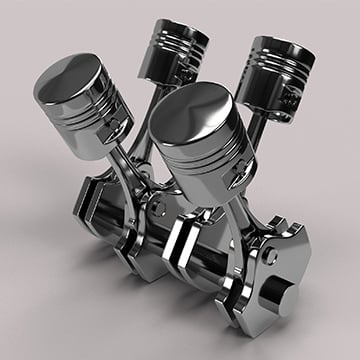
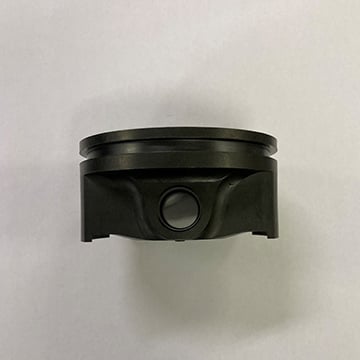
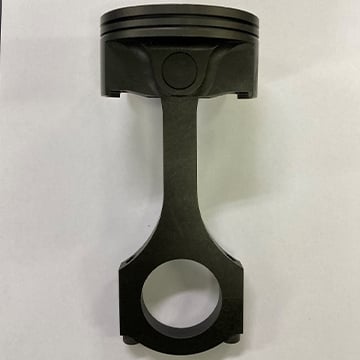
Conventional materials
Metal
Issues
High density
Required Properties
High temperature stiffness, fatigue resistance, sliding properties
Advantages with AURUM™
Reduced weight of pistons > reduced counter weight
Engines with lower weights can be proposed
Recommended grades
Oil seals for construction machinery: long-term durability
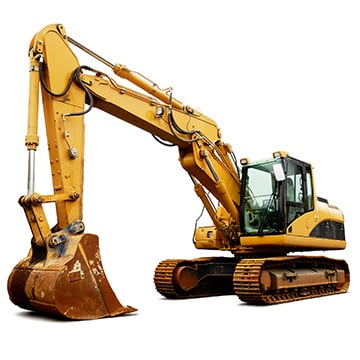
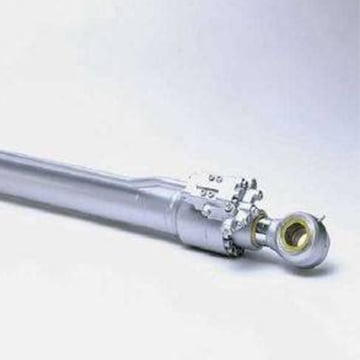
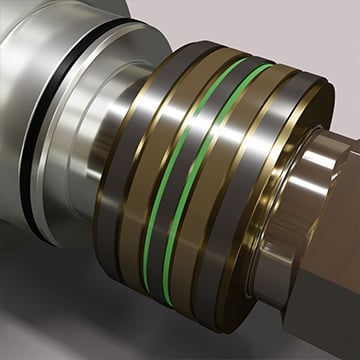
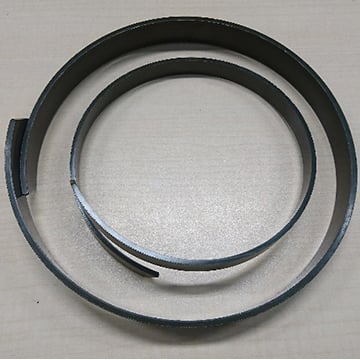
Conventional materials
Cotton phenol
Issues
Long-term durability (chemical resistance), dust generation during processing
Required Properties
Long-term durability(high temperature stiffness, sliding properties), toughness
Advantages with AURUM™
- Long-term durability(high temperature stiffness, sliding properties)
- Toughness
Long-term durability
High-quality cylinders (drastic reduction in market complaints)
Recommended grades
Structural components of aircraft engines: high temperature stiffness, chemical resistance
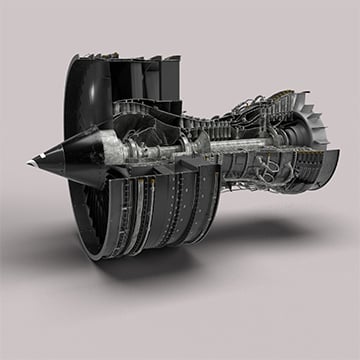
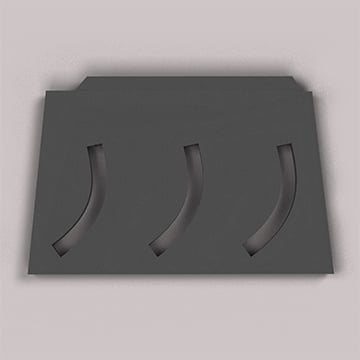
Conventional materials
Metal
Issues
Weight reduction, corrosion resistance
Required Properties
High temperature stiffness (~ 230℃), chemical resistance (MEK, acetone)
Advantages with AURUM™
- Long-term durability(high temperature stiffness, sliding properties)
- Chemical resistance
Complex shapes can be created through injection molding
Excellent high temperature stiffness is maintained even in engine environments
Recommended grades
Resin for CFRP: high temperature stiffness (high Tg)
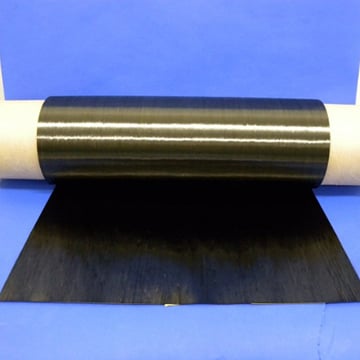
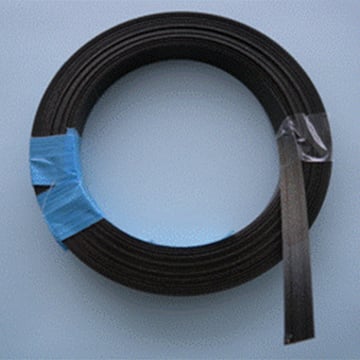
Conventional materials
Thermosetting resins, thermoplastic resins (PEEK, PEI)
Issues
Thermosetting resins: processing cycle time (long), expiration date, heat resistance
PEEK, PEI: High temperature stiffness
Required Properties
Aircraft applications: High chemical resistance (MEK, acetone, aircraft fuel), high temperature stiffness
Advantages with AURUM™
- High temperature stiffness
- Chemical resistance
- Amorphous (shrinkage factor)
- Fine powder
CFRP with excellent high temperature properties > can be applied to aircraft components and materials
Recommended grades
Electric wire coating (extrusion coating): heat resistance, extrusion coating
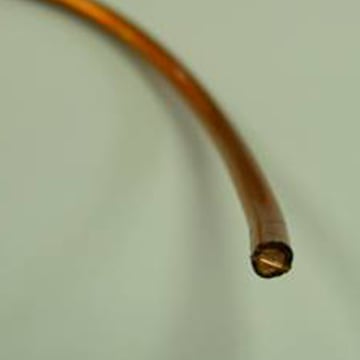
Conventional materials
PAI (polyamide-imide), thermoplastic resin (PEEK)
Issues
PAI (polyamide-imide): film formability of at least 100 μm (cost), pinholes
Required Properties
Heat resistance on par with PAI (polyamide-imide) (200℃), extrusion coating (10 - 500 μm)
Advantages with AURUM™
- Heat resistance (200℃)
- Creep resistance
- Extrusion coating
Possesses heat resistance and electrical properties comparable to PAI (polyamide-imide), and enables extrusion coating
Recommended grades
High Voltage Winding Wire:Heat resistance/Low dielectric constant/Thick layer & Mono-layer coating
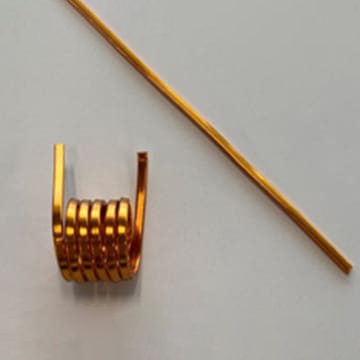
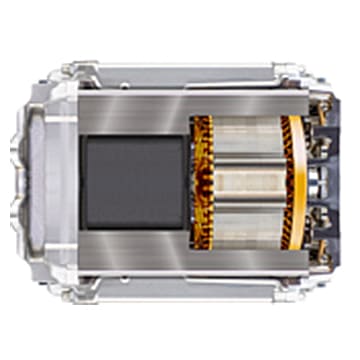
Technical trend of EV motor
Hiegher output, Downsizaion
Conventional materials
PEEK(extrusion coating)
PAI/PI varnish(dip coating)
Issues of conventional material
PEEK: Low retention rate of electrical property at High temp.(≧150℃)
Necessity of adhesive layer due to poor adhesion with copper
PAI/PI vaenish: Difficulty of thick layer coating
Less eco-frienfly due to a large amount consumption of electricity & varnish solvent
Required Properties
High retention rate of electrical property at high temp.
Adhesion with copper
Flexibility
Coating thickness accuracy
Chemical resistance
Heat aging resistance
Advantages with AURUM™
High retention rate of electrical property(low dielectric constant & high breakdown voltage) at high temp.
Extrusion coating process realizes thick layer coating ang more eco-friengly process
Mono-layer coating without adhesive layer
Recommended grades
non-reinforced grade