Lineup
Optical Grade Line-Up
Product Line-Up
Table of Product Properties

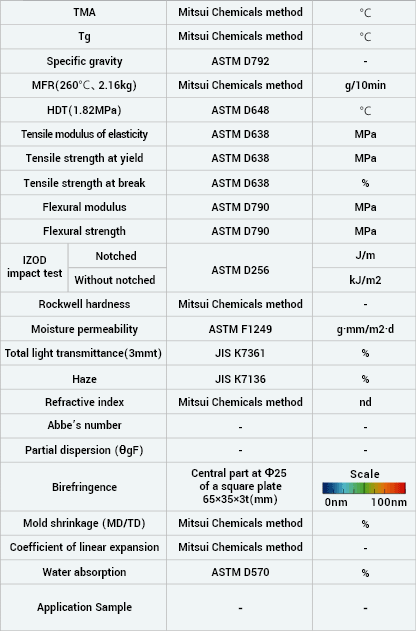
1. Injection molding machine
1-1 Selection criteria for molding machines
- ○ The molding machine size should be adequate to the product volu me. A bigger machine tends to lengthen the retention time of molten r esin, often resulting in carbonation and/or yellow discoloration of the res in.
1-2 Screw design
- ○ A lower compression ratio around 2 is preferable, but molding is possible with about 2.5.
- ○ A full flight screw is recommended to use. It is preferable that the screw head incorporates a backflow prevention mechanism (a check valve).
- ○ High shear stress at plasticization may cause discoloration and/or black spots on APEL™.
1-3 Material of screw and cylinder
- ○ Coating of non-attachment properties to molten resin is recommended to use.
- ○ Effective coating include Cr plating as well as TiN, TiCN, TiC or W2C.
1-4 Nozzle
- ○ Open type or shut-off type is useable.
2. Mold Design
2-1 Basic Structure
- ○ Mold should be designed with APEL™ mold shrinkage of 0.6%, followed by a fine adjustment. A drift angle 2°or greater should be applied, taking the mold shrinkage into consideration.
- ○ APEL™ is a resin that has a high rigidity and is low in extensibility, thus is not suitable for an undercut shape which may cause cracks on mold goods.
2-2 Material of mold
- ○ Choose a material that is suitable for thorough mirror polishing and on the mold surface of which gases resulting from molding processes are unlikely to produce tarnish.
2-3 Gates, Runners and Sprue
- ○ Shapes similar to those used for conventional resins are applicable.
- ○ A pinpoint gate is effective for reducing internal stress in the gate of mold goods and also for eliminating the need of finishing process on the gate of mold goods.
- ○ A cold runner is more recommendable than a hot runner as a hot runner may cause black spots, yellowing and/or discoloration due to retention of resin.
- ○ Round type is the most suitable for runner.
2-4 Degassing
- ○ Degassing can be done through the parting lines, but when tarnish that is likely on account of gases is recognized it will be necessary to make an approximately 0.02 mm deep ditch for degassing.
2-5 Stringiness prevention
- ○ A high nozzle temperature can cause stringiness. A sprue having a stringiness preventing function will be effective.
3. Method of molding
3-1 Pre-drying
- ○ Pre-drying of the pellets is recommended.
- ○ However, a slight amount of water on the surface of a pellet may affect the appearance of molded goods. Moreover, dissolved air in such a pellet may cause yellow discoloration and when gasified it can cause poor transcription. Accordingly, pre-drying is effective whenever a high standard appearance is required.
- ○ Pre-drying a pellet is also effective in making smooth plasticization at molding.
3-2 Material Purging
- ○ When another material has been used, it is necessary to perform a purge with a commercially available cleaning pellet that is suitable for the molding temperature or polypropylene (homo-type) for 3 to 5 kgs or so before replacing to APEL™. This should be followed by a purge with APEL™ for 2 to 3 kgs. Check for muddy or tarnished surface on the molded goods.
- ○ If purging is still insufficient, it will be effective to use glass-fiber reinforced polypropylene as a purging material or to perform a cleaning with the screw removed.
Pre-drying conditions
Grade | Temperature(℃) | Time(hrs) |
---|---|---|
APL5014CL | 110~120 | 6~12 |
APL5015AL | 120 | 6~12 |
APL5016SL | 120 | 6~12 |
APL5013VH | 100 | 6~12 |
APL5014XH | 120 | 6~12 |
3-3 Molding Conditions
[ Cylinder Temperature ]
- ○ The heat resistance of APEL™ differs according to grade, thus a cylinder temperature should be set in line with the following formula:
Cylinder temp. = APEL™ softening temp. + 100 to 130℃ - ○ Except for the space under the hopper, the temperature of each cylinder block should be set practically flat.
- ○ When temperature setting is too low and noise is heard in the cylinder, increase the cylinder temperature. Increasing the temperature in the hopper side (before screw compression section) will be especially effective.
[ Mold Temperature ]
- ○ Mold transfer performance of APEL™ tends to be affected by mold temperature. The closer the mold temperature (measured value) is to the glass transition temperature (Tg) of the resin, the better the mold transfer is. Adjust it to the Tg of the resin. (Recommended Temperature: Tg-15 ~ Tg-3℃ (Measured value)
[ Back Pressure ]
- ○ 3~5 Mpa(30~50kgf/cm²), maximum 10 MPa(100kgf/cm²)
- ○ Too much backpressure may lead to yellowing, discoloration and/or gel generation.
[ Injection Pressure ]
- ○ Holding pressure (secondary pressure) should be set as low as possible in the range of 50 to 150 MPa.
- ○ Because of high solidification speed of amorphous materials such as APEL™, too high holding pressure will cause cracks and/or leave deformation around the gate.
[ Injection Speed ]
- ○ Increasing injection speed is effective in improving mold transcription, thus improving the appearance of goods.
[ Suck Back ]
- ○ Suck-back should be avoided as much as possible.
- ○ Although suck-back is effective in preventing stringiness, by dragging air in from the nozzle it may cause bubbles and/or yellowing. If suck-back is unavoidable, make the suck-back volume minimal.
[ Screw Speed ]
- ○ If the screw speed is too high, it may drag air in and cause bubbles.
3-4 Pausing or termination of molding
- ○ Stop the molding machine to interrupt the operation for a short time.
- ○ If an interruption extends over 1 hour, lower the cylinder temperature to 170℃ to avoid burning the resin inside the cylinder.
- ○ To terminate the operation, switch off the heater after the cylinder internal area is replaced with polypropylene.
1. Injection molding machine
1-1 Selection criteria for molding machines
- ○ The molding machine size should be adequate to the product volu me. A bigger machine tends to lengthen the retention time of molten r esin, often resulting in carbonation and/or yellow discoloration of the res in.
1-2 Screw design
- ○ A lower compression ratio around 2 is preferable, but molding is possible with about 2.5.
- ○ A full flight screw is recommended to use. It is preferable that the screw head incorporates a backflow prevention mechanism (a check valve).
- ○ High shear stress at plasticization may cause discoloration and/or black spots on APEL™.
1-3 Material of screw and cylinder
- ○ Coating of non-attachment properties to molten resin is recommended to use.
- ○ Effective coating include Cr plating as well as TiN, TiCN, TiC or W2C.
1-4 Nozzle
- ○ Open type or shut-off type is useable.
2. Mold Design
2-1 Basic Structure
- ○ Mold should be designed with APEL™ mold shrinkage of 0.6%, followed by a fine adjustment. A drift angle 2°or greater should be applied, taking the mold shrinkage into consideration.
- ○ APEL™ is a resin that has a high rigidity and is low in extensibility, thus is not suitable for an undercut shape which may cause cracks on mold goods.
2-2 Material of mold
- ○ Choose a material that is suitable for thorough mirror polishing and on the mold surface of which gases resulting from molding processes are unlikely to produce tarnish.
2-3 Gates, Runners and Sprue
- ○ Shapes similar to those used for conventional resins are applicable.
- ○ A pinpoint gate is effective for reducing internal stress in the gate of mold goods and also for eliminating the need of finishing process on the gate of mold goods.
- ○ A cold runner is more recommendable than a hot runner as a hot runner may cause black spots, yellowing and/or discoloration due to retention of resin.
- ○ Round type is the most suitable for runner.
2-4 Degassing
- ○ Degassing can be done through the parting lines, but when tarnish that is likely on account of gases is recognized it will be necessary to make an approximately 0.02 mm deep ditch for degassing.
2-5 Stringiness prevention
- ○ A high nozzle temperature can cause stringiness. A sprue having a stringiness preventing function will be effective.
3. Method of molding
3-1 Pre-drying
- ○ Pre-drying of the pellets is recommended.
- ○ However, a slight amount of water on the surface of a pellet may affect the appearance of molded goods. Moreover, dissolved air in such a pellet may cause yellow discoloration and when gasified it can cause poor transcription. Accordingly, pre-drying is effective whenever a high standard appearance is required.
- ○ Pre-drying a pellet is also effective in making smooth plasticization at molding.
3-2 Material Purging
- ○ When another material has been used, it is necessary to perform a purge with a commercially available cleaning pellet that is suitable for the molding temperature or polypropylene (homo-type) for 3 to 5 kgs or so before replacing to APEL™. This should be followed by a purge with APEL™ for 2 to 3 kgs. Check for muddy or tarnished surface on the molded goods.
- ○ If purging is still insufficient, it will be effective to use glass-fiber reinforced polypropylene as a purging material or to perform a cleaning with the screw removed.
Pre-drying conditions
Grade | Temperature(℃) | Time(hrs) |
---|---|---|
APL6509T | 60 | 5~6 |
APL6011T | 80~90 | 5~6 |
APL6013T | 80~100 | 5~6 |
APL6015T | 80~100 | 5~6 |
3-3 Molding Conditions
[ Cylinder Temperature ]
- ○ The heat resistance of APEL™ differs according to grade, thus a cylinder temperature should be set in line with the following formula:
Cylinder temp. = APEL™ softening temp. + 100 to 130℃ - ○ Except for the space under the hopper, the temperature of each cylinder block should be set practically flat.
- ○ When temperature setting is too low and noise is heard in the cylinder, increase the cylinder temperature. Increasing the temperature in the hopper side (before screw compression section) will be especially effective.
[ Mold Temperature ]
- ○ Mold transfer performance of APEL™ tends to be affected by mold temperature. The closer the mold temperature (measured value) is to the glass transition temperature (Tg) of the resin, the better the mold transfer is. Adjust it to the Tg of the resin. (Recommended Temperature: Tg-15 ~ Tg-3℃ (Measured value)
[ Back Pressure ]
- ○ 3~5 Mpa(30~50kgf/cm²), maximum 10 MPa(100kgf/cm²)
- ○ Too much backpressure may lead to yellowing, discoloration and/or gel generation.
[ Injection Pressure ]
- ○ Holding pressure (secondary pressure) should be set as low as possible in the range of 50 to 150 MPa.
- ○ Because of high solidification speed of amorphous materials such as APEL™, too high holding pressure will cause cracks and/or leave deformation around the gate.
[ Injection Speed ]
- ○ Increasing injection speed is effective in improving mold transcription, thus improving the appearance of goods.
[ Suck Back ]
- ○ Suck-back should be avoided as much as possible.
- ○ Although suck-back is effective in preventing stringiness, by dragging air in from the nozzle it may cause bubbles and/or yellowing. If suck-back is unavoidable, make the suck-back volume minimal.
[ Screw Speed ]
- ○ If the screw speed is too high, it may drag air in and cause bubbles.
3-4 Pausing or termination of molding
- ○ Stop the molding machine to interrupt the operation for a short time.
- ○ If an interruption extends over 1 hour, lower the cylinder temperature to 170℃ to avoid burning the resin inside the cylinder.
- ○ To terminate the operation, switch off the heater after the cylinder internal area is replaced with polypropylene.
Catalog Download
Please download the APEL™ catalog