We are committed to reducing occupational health risks and improving working conditions by, for example, utilizing the Occupational Safety and Health Management System scheme, the harmful chemical substance risk assessment (new risk assessment system) established in fiscal 2015, through onsite inspections conducted by occupational physicians and health supervisors as well as by means of internal audits. Regarding autonomous chemical substance management, we are steadily promoting measures to prevent exposure through hazardous risk assessment and facility improvements. In fiscal 2024, we have established a new chemical substance management system, including the appointment of chemical substance manager and a person responsible for managing the wearing of protective equipment, and have begun its operation.
Occupational Health
Preventing Exposure to Harmful Substances
Risk Assessment
The reformed Industrial Safety and Health Act now requires reinforcement of risk assessments of chemical hazards and implementation of countermeasures. Our conventional risk assessment system was updated to create a new system in fiscal 2016, and we have been conducting a risk assessment of working with harmful substances (inhalant chemicals) using the new system. We have now completed all qualitative risk assessments by fiscal 2023, with the number totaling 14,294. Of these, 3,273 cases were identified as high risk, and we have completed quantitative assessments on 3,025 of these. Work procedures that have been judged to be of high risk as a result of the quantitative assessment, have been subject to methodical reforms to reduce the risks involved. In addition, we also built specific risk assessments for health problems newly caused by the absorption of chemical substances through the skin in fiscal 2018 in response to a rise in social concern about absorption of hazardous chemicals through the skin. We started these assessments in fiscal 2019, and have completed the assessments of 4,192 cases in fiscal 2023. Based on the assessment results, we are reviewing facility response and working procedures, as well as selecting protectors with more appropriate shielding and durability to reduce risks.
In fiscal 2024, a qualitative assessment will be conducted on the new work. In addition, we plan to address 248 of the 3,273 cases with high risk levels for which quantitative assessments have not yet been done.
Example of improving the working environment (1) Transfer of organic solvent
Before |
There was a risk of exposure to organic solvents when feeding organic solvents into the drum inlet.
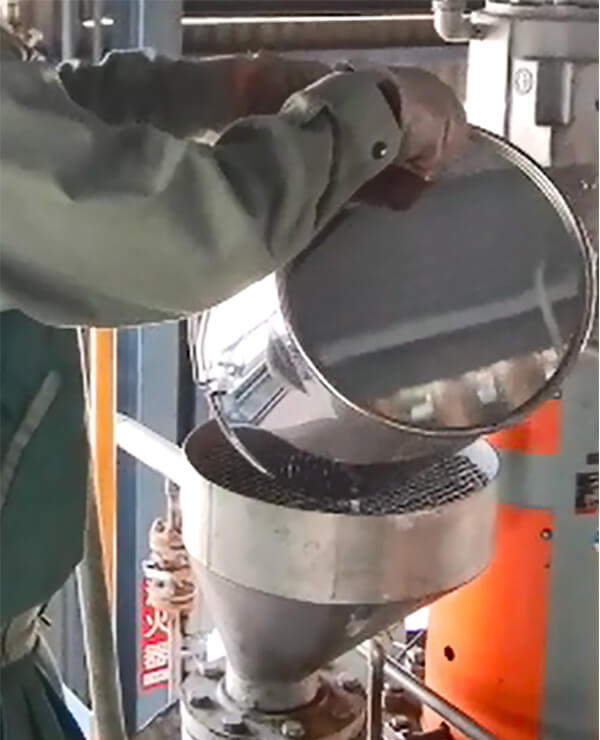
After |
The method of transferring liquid directly from drums to the drum facility using a transfer hose has been changed, eliminating the work of feeding liquid into the drum inlet.
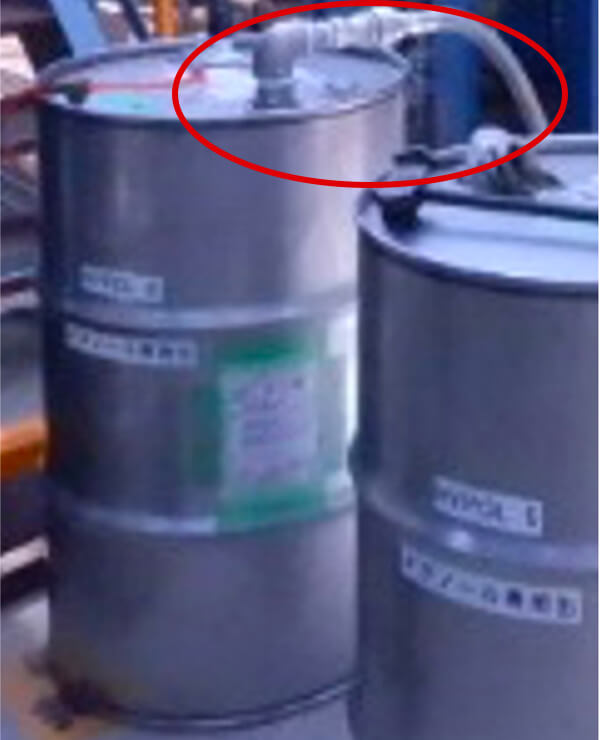
Example of improving the working environment (2) Organic solvent extraction work
Before |
There was a risk of exposure when extracting solvent into pails and disposing of liquid waste.
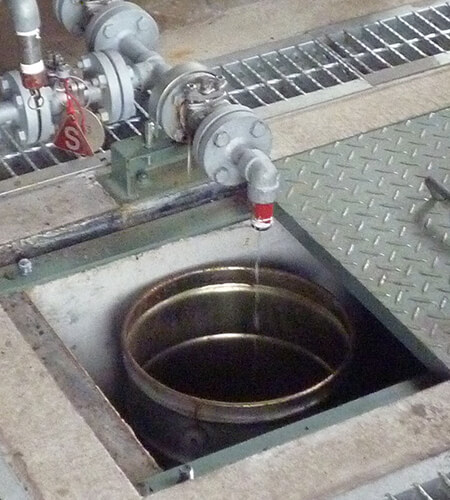
After |
A lid with a window for visual confirmation was installed on the pail so that extraction work can be performed in a nearly airtight condition. In addition, a nozzle with a cock is attached to the pail, which enables liquid waste to be discharged into a waste drum while maintaining distance from the source.
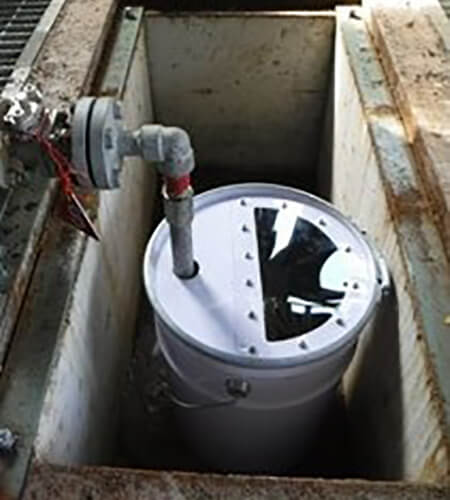
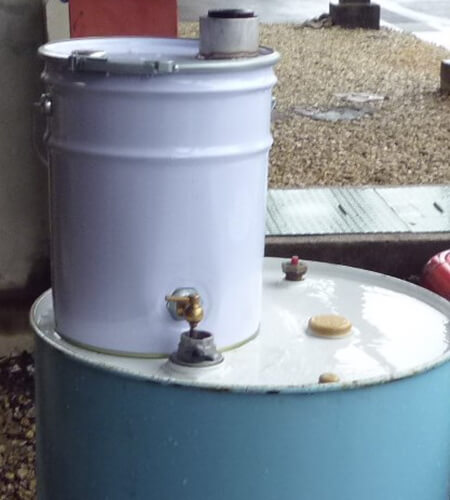
Onsite Inspections Conducted by Occupational physicians Aimed at Reducing Occupational Health Risks at Overseas Subsidiaries and Affiliates
In an effort to reduce occupational health risks at overseas affiliates, onsite inspections are undertaken on a systematic basis and steps taken to provide instructions regarding areas of occupational health improvement at the time head office occupational physicians make their rounds at overseas bases. In fiscal 2023, the program was implemented at four overseas business sites and training was provided to local personnel.