Regarding the issue of plastics, which are mainstay products of the Mitsui Chemicals Group, we are focusing on a biomass strategy and a recycling strategy that cover the entire supply chain. By implementing these two strategies and addressing the problem of plastic waste, we will continue to promote resource recycling and endeavor to create a circular economy.
Endeavor to create a circular economy
Biomass strategy and Recycling strategy |
Biomass strategy and Recycling strategy |
Biomass strategy: Expanding lineup of bio-based plastic products
Bio-based plastics made from plants—which grow by absorbing CO2— and animals are attracting much attention as a possible substitute for conventional petroleum-derived plastics. As we believe that a shift to bio-based raw materials encourages resource recycling, curbs the further use of fossil resources, and therefore helps mitigate climate change, we aim to expand our lineup of bio-based plastic products.
As a materials manufacturer that supports people’s life infrastructure, the Group has launched a brand with the key messages of “we explore the materials of materials” and “we’re reshaping the world from a material level”—BePLAYER™, which achieves carbon neutrality with biomass. The new brand is another part of our efforts to bring about reductions in GHG emissions across society.
The Mitsui Chemicals Group has procured and introduced bio-based hydrocarbons as feedstock for our naphtha crackers at the Osaka Works ethylene plant. At the same time, we are producing and marketing chemicals such as phenol and acetone, as well as plastics products such as polyethylene and polypropylene under the mass balance approach, which allows for the attribution of bio-based content to specific products. In order to expand the lineup of bio-based hydrocarbon derivatives that we can offer, we are currently in the process of obtaining International Sustainability & Carbon Certification (ISCC) PLUS certification for a variety of our products. As of September 2024, we have received certification for approximately 40 products, including products made from naphtha and products further downstream. Through our collaborations with partners like Teijin Limited, which uses the Group’s biomass-derived bisphenol A to develop and produce biomass-derived polycarbonate resins, and efforts to promote sales of BePLAYER™ products, we will establish a social foothold for biomass and propel the spread of both bio-based chemicals and bio-based plastics.
Prasus™, a mass-balanced bio-polypropylene (PP) manufactured and sold by Prime Polymer Co., Ltd.—a Mitsui Chemicals Group company—has been adopted by the Japanese Consumers' Co-operative Union for use in food packaging, becoming the first plastic container and packaging using bio-attributed plastics to receive the Eco Mark*.
*Eco Mark:
An environmental label that is given to various products and services operated by the Japan Environment Association, which are recognized as having a low environmental impact throughout their life cycle from production to disposal and as being useful for environmental preservation. Bio-attributed plastics (i.e., bio-based plastics produced under the mass balance method) were newly added to the Eco Mark certification criteria on February 1, 2023.
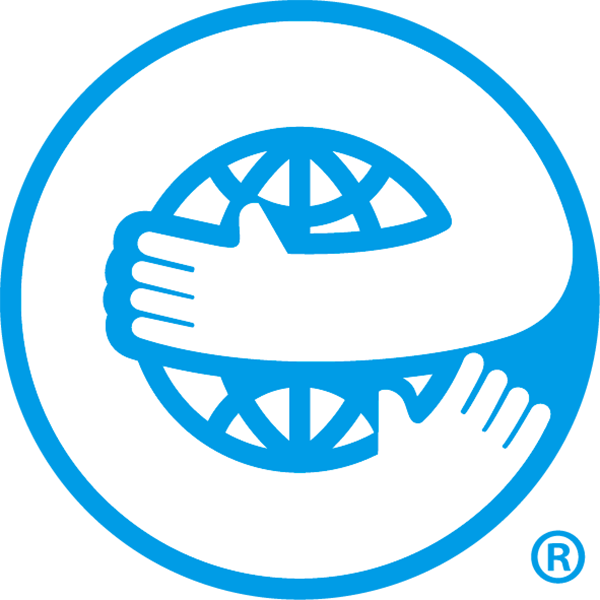
Mass balance method
Mitsui Chemicals produces bio-based chemicals and plastics by mixing fossil-derived naphtha with bio-based hydrocarbons in the manufacturing process. These products are made of mixtures of fossil-derived and bio-based raw materials, but we allocate the share of bio-based raw materials used during production only to specific products and provide them to customers. This method is called the mass balance method. By using this method, a portion of the finished product can be considered “100% biomass-derived” depending on the amount of biomass-derived feedstock input, thus making it possible to meet the diverse biomass product needs of customers. We have acquired a third-party certification (ISCC PLUS certification) to prove that we properly manage and run the mass balance method in a reliable way. The Group believes that this method will play an important role not only for biomass products, but also as a scheme to help expand the portfolio of recycled chemical products.
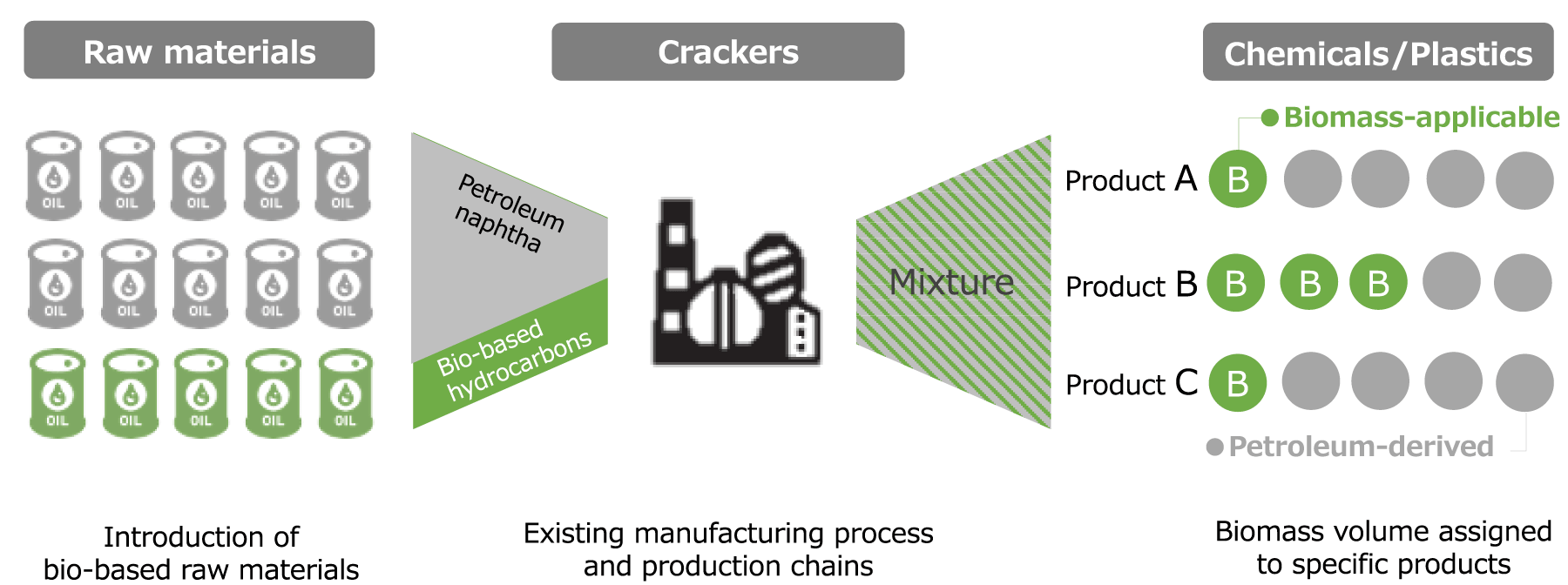
Recycling strategy: Promoting plastic recycling
As social issues related to waste management, such as resource depletion and the problem of plastic waste, become more serious, the Group considers waste plastics and other materials as resources, and is promoting initiatives to effectively utilize them. Resource recycling not only helps reduce the use of fossil materials and fuels by efficiently utilizing such resources, but it also decreases waste plastic and GHG emissions throughout the value chain. Through the development of new materials, recycling systems, and value chains, we will make the circle of the circular economy bigger and broader, such as through chemical and material recycling of waste plastic, development of mono-material packaging, and support for startup businesses.
The Mitsui Chemicals Group has begun Japan’s first manufacturing and sales of chemically-recycled derivatives (chemicals and plastics) based on the mass balance approach, using pyrolysis oil produced from plastic waste and procured from CFP CORPORATION as a feedstock for the cracker at the Osaka Works since March 2024. This initiative will make it possible to adapt materials derived from recycling processes in applications where such materials could not conventionally be used due to quality or hygiene considerations. The move could potentially result in a substantial increase in the recycling rate of plastics, which has been low to date. In addition, with this technology, as plastic waste is pyrolyzed into hydrocarbon oil and fed into the cracker, the most upstream part of our operations, the physical properties of the derivatives (chemicals and polymers) are equivalent to those of more conventional products made from virgin materials.
Combined with our December 2021 introduction of bio-based hydrocarbons to a cracker, this latest initiative marks the achievement of Japan’s first bio & circular cracker. The project is emblematic of our efforts to transition away from petroleum-based raw materials, and will help bring about a society that is not just sustainable but regenerative.
Chemical recycling flowchart
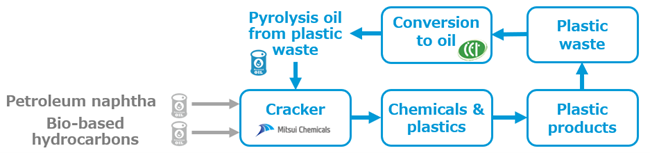
The Mitsui Chemicals Group has developed and provided the digital resource circulation platform RePLAYER™ Blockchain Platform as a solution to promote the recycling of plastic materials. This platform ensures the traceability of recycled plastics by linking and storing a range of information necessary for the recycling of plastics, such as the information on materials, the information on physical properties, information on quality, the ratio of recycled materials, and the number of times recycled, with manufacturing numbers or serial numbers in each phase of the supply chain. In addition, the platform has enabled us to provide recycled materials that are safe and secure in terms of protecting information and ensuring authenticity through an effective use of the blockchain technology.
Moreover, the Mitsui Chemicals Group, as the leading company, established the Pla-chain Consortium jointly with IBM Japan, Ltd. and Nomura Research Institute, Ltd. to realize a resource recycling-oriented society. The consortium has been striving to form a partnership beyond the boundaries of industries to promote the use of recycled plastics with a focus on traceability (51 companies have joined the partnership as of June 2024).
The Group has launched the RePLAYER™ initiative, which aims to contribute to a circular economy via recycling by using waste plastic and other waste as resources. As part of the effort to realize a circular economy, we are currently working on the RePLAYER™ Renewable Plastics Layer System to test the mechanical recycling of flexible packaging. The system serves to recover film waste after printing from converters, remove the ink, and then pelletize the waste before turning it back into flexible packaging film. Using facilities for the system at the Nagoya Works, we plan to accelerate development of recycled materials technologies suited to flexible packaging films, further expand our collection of film waste, and begin providing samples of recycled materials.
In December 2022, Toppan Inc., RM Tohcello Co., Ltd., and Mitsui Chemicals began discussing the basis of the joint pilot testing, and in August 2023, the three companies shifted to a full-fledged joint pilot testing, with BOPP film waste – generated by Toppan from processes such as printing adjustment – being recovered by Mitsui Chemicals, which also removes the film waste’s printing and converts it into pellets that are in turn made into recycled BOPP film by RM Tohcello. Toppan is also evaluating the recycled BOPP film’s quality, including its suitability for printing, lamination, and the creation and filling of flexible pouches. Through this initiative, the three companies aim to have this technology implemented in society by fiscal 2025 in line with the milestone laid out by the Ministry of the Environment’s Resource Circulation Strategy for Plastics.
Renewing the world from the material of materials. BePLAYER™ and RePLAYER™ for regenerative lifestyles.
A significant social transformation is necessary to realize carbon neutrality and a circular economy society. As a materials manufacturer that supports life infrastructure of the population, the Mitsui Chemicals Group has the potential to change people’s lifestyles from the ground up. Recognizing this strength and purpose, we have the responsibility to broadly provide cross-Group solutions to society. In order to fulfil this responsibility, it is important to continue proactive communications and gain societal recognition as a comprehensive solutions company in the field of carbon neutrality and circular economy. To this end, the Group has launched two brands with the key messages of “we explore the materials of materials” and “we’re reshaping the world from a material level”—BePLAYER™, which achieves carbon neutrality with biomass, and RePLAYER™, which creates a circular economy through recycling. By promoting both of these solution brands, which aim to utilize renewable resources and manage stock resources, we aim to resolve multi-faceted and complex social challenges, and take sustainability a step further and provide regenerative lifestyles from the material level.
Looking back, the history of Mitsui Chemicals is also a history of switching to alternative raw materials. Starting with the production of chemical fertilizers from the byproduct gas of coal coke in 1912, we have expanded our business while switching raw materials and shifting to the chemical business using gas and petroleum naphtha as raw materials. Now is the time for a shift to the chemical business using biomass and recycled resources as raw materials. With the two brands at the center of communications with society, we aim to contribute to the realization of carbon neutrality and a circular economy society and achieve further growth by once again switching to alternative raw materials.
Problems with plastic waste
The problem with plastic waste stems from plastics that have escaped from the process for resource recycling and ended up in marine environments due to inappropriate waste management. Preventing plastic waste from leaking into rivers and the sea is of utmost importance and requires a united effort by companies in the entire plastics value chain.
We have worked to manage plastic waste properly and promote its recycling by participating in global and Japanese alliances such as the Alliance to End Plastic Waste (AEPW) and Japan Clean Ocean Material Alliance (CLOMA).
Established in 2019. Signatories to the AEPW include global companies involved in the plastic value chain, such as chemical and plastic manufacturers, retailers, and waste management companies across the world. The Alliance is committed to the goal of investing $1.5 billion until 2024 to help end plastic waste and contribute to a sustainable society by driving progress in four key areas: infrastructure development to manage waste, innovation, education & engagement activities and clean-up activities.
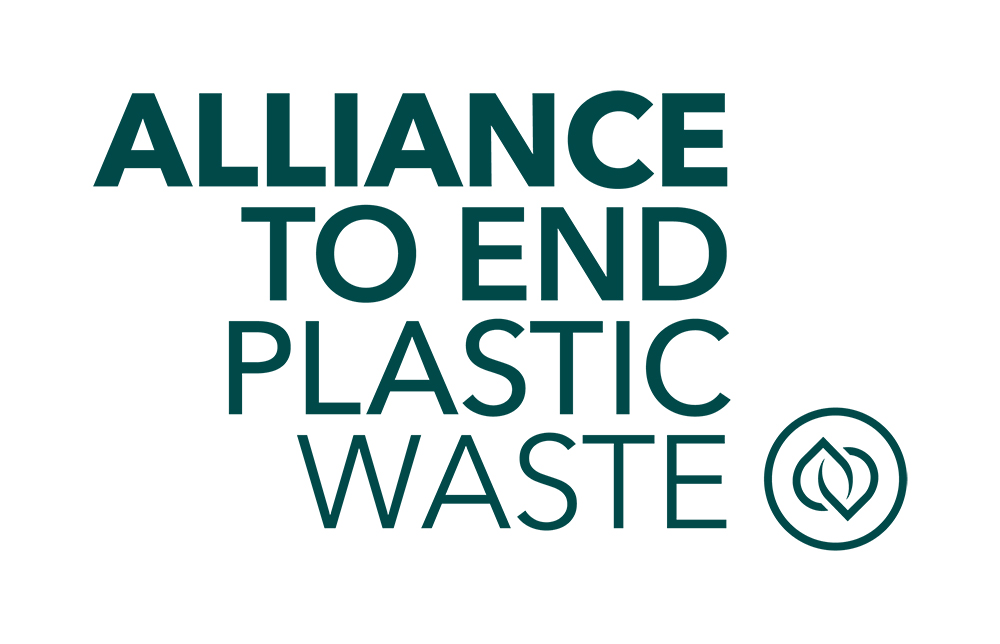
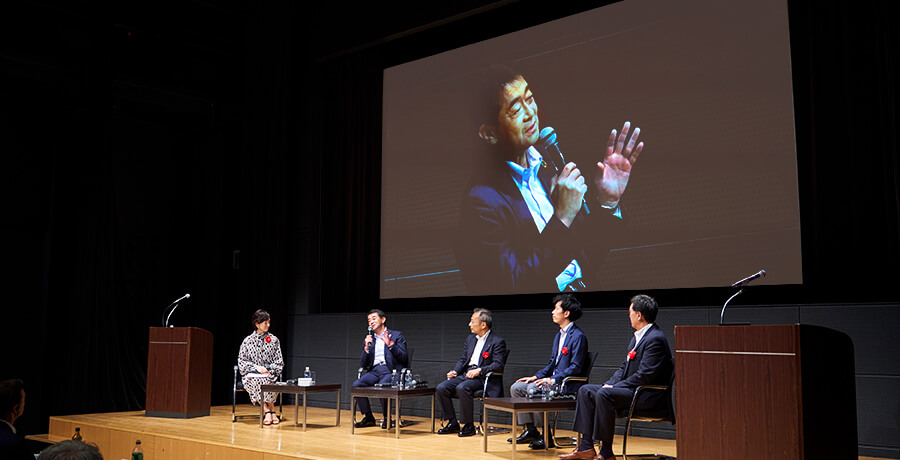
The Alliance was established in January, 2019 as a platform for strengthening coordination among a broad range of interested parties across various industries. To date, the organization has engaged in technical information sharing among members and organized partner matching opportunities. In May 2020, the CLOMA Action Plan was released with the aim of achieving a package recycling rate of 60% by 2030 and a plastic product recycling rate of 100% by 2050. The activities it specifies include studying concrete measures and plans for demonstration tests.
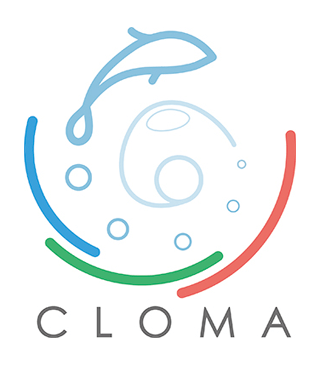