We conduct highly effective quality audits and enhance the human resource development programs to improve quality management levels.
Quality of Products and Services
Initiatives
Improving the Standard of Quality Management
Quality Training
We implement a variety of quality training programs. For example, as a human resource development program, we conduct product quality training for each level of employees from new hires to management, hold product quality lectures on the topic of "creating value that satisfies customers," and utilize teaching materials that prevent human error. There are 20 e-learning courses on quality that are available not only for domestic companies but also for overseas affiliates in multiple languages. Moreover, we have been implementing frontline measures to prevent quality issues on the shop floor (QRG activities) with the aim of identifying and eliminating risks that could lead to quality issues. We are implementing these measures in our subsidiaries and affiliates.
Examples of e-learning courses | FY2023 participants (hours) (Mitsui Chemicals, Inc.) |
---|---|
Compliance of quality with laws and rules | 5,533 (2,305 hrs) |
Basic Training for quality management | 2,138 (1,247 hrs) |
Basic training for quality control methods | 804 (4,402 hrs) |
Award for Quality Management Activities in the Mitsui Chemicals Group
We run the Award for Quality Management Activity in the Mitsui Chemicals Group scheme each November, which is an industry-designated quality promotion month. We award efforts to revitalize Responsible Care (RC) activities to improve our chemical substances management level and quality management at Mitsui Chemicals and its domestic and overseas affiliates. We give awards to those who have achieved outstanding results across our workplaces to support and stimulate RC activities.
Award for Quality Management Activity in Mitsui Chemicals Group in Fiscal 2023
General Manager’s Prize of the RC & Quality Assurance Division | Description of activities |
---|---|
Phenols Division, branches (Nagoya, Osaka, Fukuoka), Ichihara Works, Osaka Works, Iwakuni-Ohtake Works | Establishment and implementation of a new system to achieve a 100% delivery specification conclusion rate |
Outstanding Technology Award | Description of activities |
Japan Composite Co., Ltd. | Reduction of foreign material complaints on compound material products |
Outstanding Achievement Award | Description of activities |
Saxin Corporation | Leveling of operations and streamlining customer documentation by making members of RC department multi-skilled |
Prime Polymer Co., Ltd. | Proactive generation and transmission of product safety information internally and externally |
Mitsui Chemicals Operation Services Co., Ltd. Prime Polymer Co., Ltd. | Continued efforts to address the black spot foreign matter problem at manufacturing plants |
Grand Siam Composites Co., Ltd. | Investigation of the cause of bronzing*1 and enhanced quality control system against bronzing defect on instrumental panel part |
Special Award | Description of activities |
Nagoya Works | Continuous quality improvement of electrolyte (Millet™) through IATF16949*2 operations |
*1 Bronzing:
A phenomenon in which a gold-like metallic luster appears on the surface of a coating
*2 IATF16949:
An international standard for quality control of automotive products
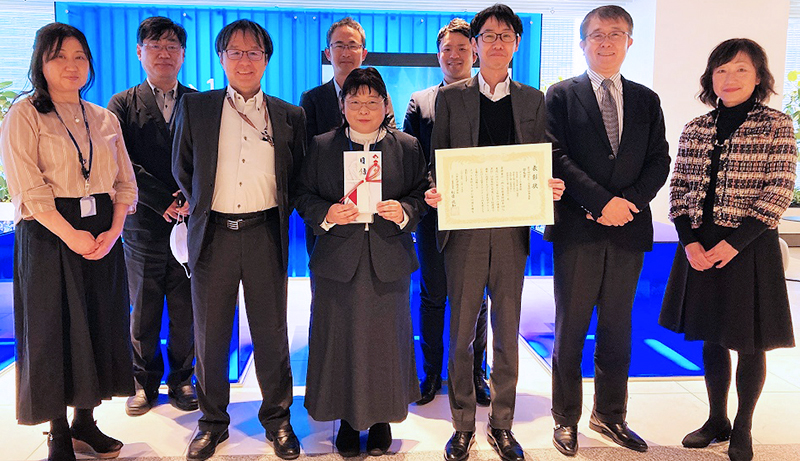
Responding to the voices of our customers
We collect customer complaints about Mitsui Chemicals products and services in the internal workflow system so that we can monitor the type of complaint, the cause and the customer’s response. The data is analyzed each month to review the situation for that year and KPIs are identified for our quality management targets for the following fiscal year.
Whenever we receive a complaint about our products or services from one of our customers, the Business, Manufacturing and Logistics Divisions work together with the Quality Assurance Division to identify the cause of the complaint and to take corrective action. In this way, every effort is made to implement preventive measures across the organization as a whole. In one such initiative, all members of the Quality Assurance Division reassess the root cause of each complaint, consider appropriate countermeasures and monitor progress every week. At the same time, we endeavor to extract important case studies, particularly where there is a substantial risk of inconveniencing our customers, or where the potential exists for similar cases to arise. These case studies are then shared across the relevant departments in the monthly quality management report.
In the face of the demand for a higher level of chemical management (for chemical substances in products), we support product stewardship and implement chemical substance management throughout the entire supply chain. We respond swiftly and accurately to enquiries from customers about chemical substances in our products by organizing the information in a database and designating a department to manage it.
Activities to Ensure Quality Compliance
Recently, serious quality-related compliance violations have been identified at domestic and overseas affiliates. In light of these events, the Mitsui Chemicals Group is working on measures to strengthen quality compliance observance. Specifically, we are proceeding with countermeasures to respectively address “motivation”, “opportunity”, and “rationalization,” known as the fraud triangle, in accordance with our basic policy. Furthermore, horizontal application of such activities includes revising and reiterating the "Guidelines for Ensuring the Soundness of Product Inspections," strengthening items from a compliance perspective in quality audits, bringing forward audits to new affiliates, holding quality dialogues targeting "affiliates at high risk of quality issue," and inspecting the management status of obtaining and maintaining product certifications.
Measures to Strengthen Quality Compliance Observance (Basic Policy)
- Motivation: Creating a quality system that satisfies customers
- Opportunity: Creating a system that does not/will not allow falsification
- Rationalization: Fostering a compliance-oriented organizational culture and sense of ethics through education and awareness-raising activities
Response to the New Business
We have established a quality management system to meet the demands of customers and society for the solutions-based business and new businesses with social issue perspectives, and have started their operations. This initiative consists of "contributing to the creation of value for customers' products" by linking customer feedback to development goals and "preventing defects at the customers' end" at the development phase. In addition, the Mitsui Chemicals Group is taking steps to also ensure compliance with all applicable statutory, regulatory, and certification requirements for each product purpose and conducts risk assessments before bringing a particular product to the market. It is through these activities that we are strengthening our trust-based relationships with customers and ensuring quality in new businesses.
We established a designated group to address compliance issues in connection with laws, regulations, and certification related to pharmaceutical affairs, including the medical instruments business. With this designated group taking the lead, every effort is made to confirm the safety and efficacy of products. Steps are also taken to strictly comply with all statutory and regulatory requirements.