The Mitsui Chemicals Group is implementing various initiatives, including training and drills, toward nurturing human resources with a high awareness of dangerous situations and the ingraining of a safety culture throughout the Group.
Safety and Prevention
Safety Education and Training
Emergency Drills
The Mitsui Chemicals Group systematically conducts emergency drills in Works to prepare for accidents, earthquakes, and tsunamis.
Envisioning emergency situations, such as a fire or leakage of hazardous substances, our Works regularly conduct comprehensive disaster prevention drills jointly with municipal fire and police departments. Such drills test the emergency response procedures, help make improvements when a deficiency is found, and enhance our defense capabilities through collaborations with the local authorities. Those Works located within petrochemical complexes also conduct joint disaster prevention drills with neighboring corporations and fire departments as a mutual support scheme. Affiliates in Japan and overseas conduct drills suited to their laws and work environments in preparation for their differing emergency situations. We also conduct emergency shutdown drills and evacuation drills in preparation for natural disasters, by taking into account recent large earthquakes and tsunamis.
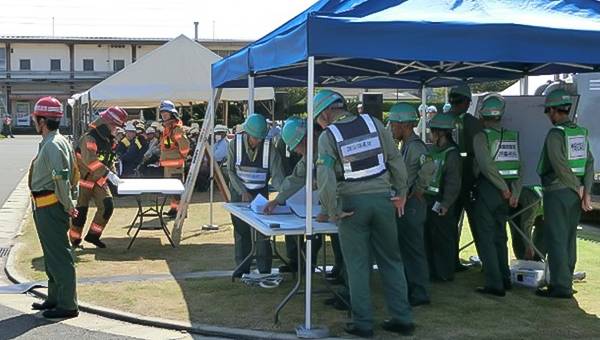
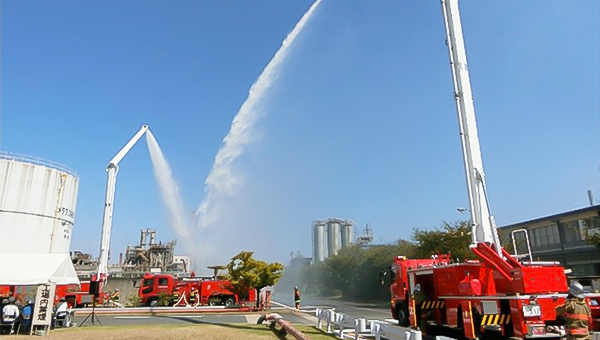
Joint drill with neighboring companies to simulate a fire caused by the leakage of hazardous materials due to an earthquake (Osaka Works)
Skill Improvement for Self-defense Firefighting Units
Mitsui Chemicals’ Ichihara Works, Osaka Works, Iwakuni-Ohtake Works, and Omuta Works are equipped with self-defense firefighting units. The unit members are regularly trained in preparation for an emergency.
In recognition of the results of daily training, the Iwakuni-Ohtake Works and Osaka Works received the Minister of Internal Affairs and Communications Award (Excellence Award) in the "Skills Contest for Self-Defense and Disaster Prevention Organizations at Petroleum Industrial Complexes" held in fiscal 2023 by the Fire Defense Agency, Ministry of Internal Affairs and Communications. This skills contest has been held since fiscal 2014 to inspire self-defense firefighters, as well as motivating them to continue to improve their skills. The participants complete safety, reliability, and promptness of their performance by conducting a procedure of releasing foam water from a height onto a simulated fire at a hazardous facilities. This is our 10th consecutive year to receive an award since the contest began. We continue improving our firefighting skills through determined training to contribute to the safe and stable operations of our Works.
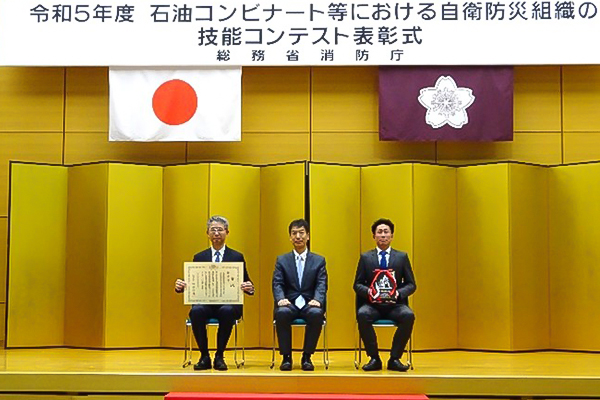
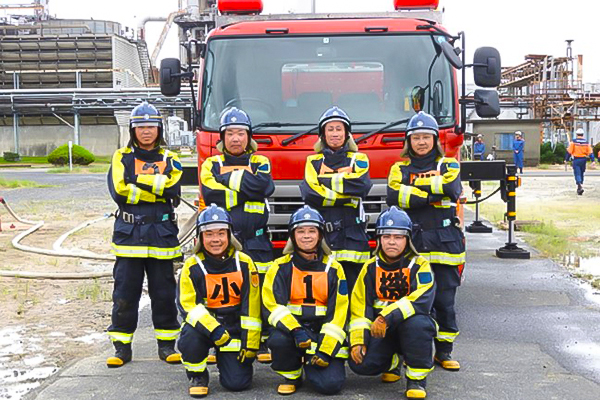
Iwakuni-Ohtake Works self-defense firefighting unit at the award ceremony and in the skills contest
Risk Prediction Training
The Mitsui Chemicals Group continues to implement risk prediction training at each of its Works based on the belief that it is important to develop human resources capable of recognizing hazards as dangers and taking safety actions to prevent them.
In addition, with regard to risk prediction and Pointing-and-Calling training for domestic and overseas affiliates, the Safety & Environment Technology Division provides training support on an ongoing basis. Through this support, we are working to ensure that all of our affiliates understand the significance and necessity of risk prediction activities and Pointing-and-Calling so that they can use and entrench them in their actual work situations. The training is also held online and incorporates exercises, presentations, and team discussions that are appropriate to actual work situations. It looks back on their daily tasks and raises awareness so that safer actions can be taken. Key men are of necessity to entrench risk prediction and Pointing-and-Calling, and the Company is encouraging their development through training.
Risk prediction training sessions
Number of Attendees (Total Training Time) | |||
---|---|---|---|
FY2021 | FY2022 | FY2023 | |
Mitsui Chemicals, Inc. | 1,591 (2,227hrs) | 1,426 (2,096hrs) | 1,906(2,630 hrs) |
Domestic Subsidiaries & Affiliates | 58 (116hrs) | 81 (138hrs) | 83(199 hrs) |
Overseas Subsidiaries & Affiliates | 18 (36hrs) | 113 (226hrs) | 256(742 hrs) |
Total | 1,667 (2,379hrs) | 1,620 (2,460hrs) | 2,245(3,571 hrs) |
Advanced Engineering Education and Passing on Technology
Mitsui Chemicals is actively engaged in various measures to foster engineers with specialized knowledge, technology, and skills, as well as to steadily pass on technology to the next generation, as part of its human resource development system based on the personnel system.
Specifically, the systematic passing of technology and development of human resources are stipulated in job descriptions and job classification tables for skilled employees, and the system clarifies the passing of technology as part of the job and holds employees accountable for their efforts.
In addition, we have defined our development plan up to the point where they assume key roles in Works under the “Production Engineering Human Resource Development Plan” to clarify the abilities and skills required to carry out their respective duties. We have also established an education system and the curriculum necessary for acquiring these abilities and skills as an “Annual Education Plan,” and provide step-by-step education through company-wide and plant collective education, e-learning, and various other off-the-job training programs, as well as through rotations and on-the-job training.
In our training, we place particular emphasis on problem-solving and accident case study education. Through factor analyses and accident case study discussions based on actual trouble cases that have occurred at production sites, we cultivate the sensitivity to identify potential sources of danger.
Small Group Activity Leader Training
Each Mitsui Chemicals Works implements small-group activities to promote problem solving and operational improvement, and provides training to the leaders of these activities. Through training by external instructors twice a year, we strive to understand our role as facilitators of activities and how to proceed, and to acquire problem-solving techniques such as QC stories and the seven QC tools, which we use in actual small-group activities. This is done in order to solve various problems and issues, improve operations and quality, and more.
The Best Plants Awards
The purpose of the Best Plants Award is to revitalize Works by honoring the excellent production sections for their activities related to safety, health, environment, quality and production technologies. Having started this system in fiscal 2004, Mitsui Chemicals has been focusing since fiscal 2013 on not only safety performance but also on the process of safety efforts, and evaluates the efforts made by the production sections and the hardships that they face.
In fiscal 2023, one was selected from among the domestic and overseas production sites for the President's Awards and six for Production & Technology Center Executive's Awards. The Company’s global expansion is advancing due not only to the Mitsui Chemicals but also to award-winning domestic and overseas affiliates.
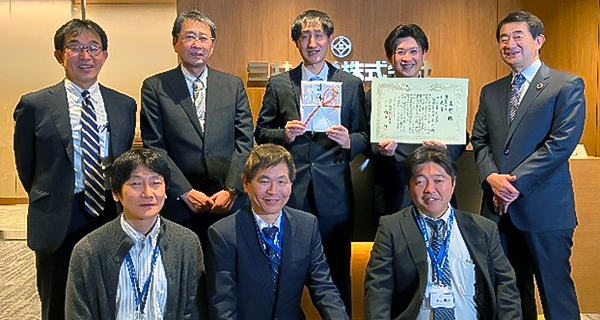
Education for Entrants
To ensure thorough safety management within the premises, all employees working at our factories, including contractors, are required to undergo entry education at the time of entry. This includes detailed explanations of the handling of construction vehicles and tools brought in, as well as tips for construction and on-site work, illustrated with specific examples. By ensuring that everyone working on the premises shares a common awareness of safety, we are committed to diligently pursuing the achievement of zero accidents and occupational injuries by accumulating safe days, one day at a time.