The Mitsui Chemicals Group positions as KPIs and monitors major accidents, the number of abnormal conditions/accidents as well as the occupational injury frequency rate.
Safety and Prevention
Accidents and Occupational Injuries
Achieving Zero Major Accidents and Serious Occupational Injuries
The Mitsui Chemicals Group is promoting initiatives for safe facilities and operations with the aim of achieving zero major accidents and zero serious occupational injuries.
Risk Prediction as well as Pointing-and-Calling
In order to eliminate accidents and occupational injuries at the Mitsui Chemicals Group, we undertake initiatives at the Works and at domestic and overseas affiliates to entrench and thoroughly implement risk prediction and Pointing-and-Calling.
Risk prediction trainers are chosen at each Works to become drivers of these risk prediction initiatives, and company-wide meetings are held once a year to exchange opinions and share activities.
The Safety & Environment Technology Division provides training support on an ongoing basis for our affiliates. Through this support, we are working to ensure that all of our affiliates understand the significance and necessity of risk prediction activities and Pointing-and-Calling so that they can use and entrench them in their actual work situations.
Near-miss Activities
At each Mitsui Chemicals Group production site, information on workers’ narrowly avoided major accidents or disasters, or “near-misses,” that occur as a result of operations, is identified, and the details are shared within the organization. These sharing activities are ongoing. Specifically, in line with the occupational safety and health management system for each production site, the organization determines the cause of these near misses, as well as preventive measures. Relevant parties are provided with the lessons learned, and plans are put into effect that cover both concrete matters, as well as more intangible issues, in the course of operations. We then ensure that the necessary resources are still available to implement the preventive measures that we have formulated.
Small-group Activities
Our Works conducts small-group activities in which small groups of people work together to solve issues or matters such as enhancing production workplace capabilities, refining mindsets and human resources development, revitalizing the workplace, and improving the business, in consideration of the characteristics of a Works.
Through these initiatives, we are united in our efforts to improve the bottom line of plant revitalization. We also share the results of the small-group activities throughout a Works by means of presentations, and the honoring of best practices leads to heightened motivation.
We held a company-wide presentation of small-group activities in October of fiscal 2023. Connecting the Head Office, Mitsui Chemicals Works, and domestic subsidiaries and affiliates online, those who attended actively asked questions and made comments in response to the presentations from each site. We share the contents within the Group and promote the revitalization and improvement of workplaces and Works as a whole.
Examples of Other Initiatives
In addition to the above, the following initiatives are routinely implemented.
- Thorough enforcement of basic safety rules stipulated in company rules, etc.
- 5S Activities
- Ensuring the wearing of protective equipment
- Mutual attention
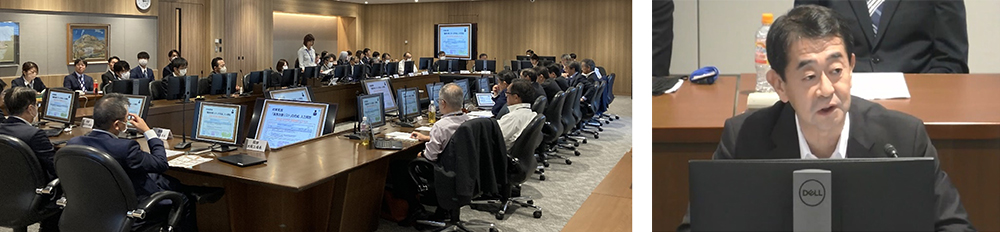
Ensuring the Reliability and Soundness of Facilities
The Mitsui Chemicals Group introduces and maintains equipment that ensures safe and stable operation.
When introducing new facilities, we not only satisfy the relevant laws and regulations, but also design them in accordance with company rules based on our experience and accumulated technology, and introduce facilities that prevent accidents such as fires, leaks, and explosions through repeated change management based on various technical evaluations.
After an equipment is installed, we formulate maintenance plans and conduct periodic inspections and regular maintenance from the perspective of preventive maintenance.
In recent years, many of our facilities have been in operation for more than 40 years. While focusing on countermeasures against age-related deterioration, we have worked on developing appropriate maintenance plans, improving construction quality, and strengthening change management to maintain and improve the reliability and soundness of our facilities.
In addition, beginning in fiscal 2023, we are stepping up our efforts to eliminate problems involving high-value losses with the goal of investing limited resources efficiently and effectively. Priority will be given to older plants where problems concentrate and to key plants that suffer significant opportunity losses when problems occur, and focus on improving technologies and addressing aging facilities. Furthermore, by actively adopting advanced technologies that are becoming practical due to recent technological advancements, we will seek to streamline and optimize our design, construction, and maintenance operations.
Furthermore, these efforts not only prevent accidents, but also contribute to environmental protection by reducing noise and odor and preventing leaks.
The aim is to further improve the reliability and soundness of facilities by strengthening the PDCA (Plan-Do-Check-Action) cycle of maintenance operations to increase efficiency and optimization from design to maintenance operations, and by proactively introducing advanced technologies. |
Evaluation of Construction Subcontractors and Support for Improvement
In order to ensure the safety, security, and quality of construction work, we have established "Guidelines for Evaluating Construction Subcontractors" and conduct evaluations of construction subcontractors contracted at Works once a year in principle. After the evaluation, we analyze the results, identify common and individual issues by construction subcontractor, and provide feedback to as well as guidance for improvement as necessary.
Key Evaluation Elements
- Safety, health and environment
- Construction quality
- Technical and mobilization capabilities, process management
- Serious negligence and defects, compliance
Major Accidents and Abnormal Conditions/Accidents
In fiscal 2023, the Mitsui Chemicals Group reported zero major accidents*1 and met its target of zero. In addition, the number of abnormal conditions and accidents*2 increased from the previous year to 16, not meeting the target of 8 or fewer. There were nine incidents of leakage and seven incidents of small fires, and countermeasures to prevent their recurrence are an issue. To prevent recurrence, for leakage, we are working on (1) developing appropriate maintenance plans, (2) reinforcing change management (risk assessment), and (3) improving the quality of construction. With regard to small fires, given that small fires in electrical equipment have been seen in a number of cases, we are promoting (1) alerts regarding electrical fires and (2) a review of equipment inspections.
*1 Major Accidents:
Accidents and abnormal conditions with a severity level of 18 points or more, as specified by the Japan Petrochemical Industry Association (JPCA) under the Center for Chemical Process Safety (CCPS) evaluation procedures, or events that involve death.
*2 Abnormal conditions/accidents:
Events that were legally handled as an abnormal condition or accident among the reported explosions, fires, leakages, bursts, breakages, or abnormal reactions.
However, such abnormal conditions or accidents exclude leakage of CFCs and small amount leakages.
Number of Major Accidents and Abnormal Conditions/Accidents
*Including subsidiaries and affiliates within our Works, and the Works general manager bears the responsibility for Responsible Care implementation.
Occupational Injuries
In fiscal 2023, the Mitsui Chemicals Group reported zero serious occupational injuries*1 that must not occur, meeting its target of zero. Compared with the Japanese overall industry average and the Japanese chemical industry average, we maintain a high level in terms of Days Away from Work Cases (DAFWCs) and, in aiming to achieve the world's highest standards for safety, targets a frequency of 0.15 or below with regard to Work-related Significant Occupational Injuries*2. For the significant occupational injury frequency, which Mitsui Chemicals emphasizes, we achieved the target value of 0.15 or less. We believe that this comes as a result of our painstaking efforts to maximize safety activities, which we have continued over the years. However, our domestic and overseas affiliates and construction subcontractors did not meet the target. We will continue to work to ensure that our safety culture is shared by the entire group and to cultivate human resources who are highly sensitive to danger, with a particular focus on incidents that could easily result in severe occupational injuries. These include "crashing and falling" and "being caught or entangled in machinery." Regarding construction subcontractors, we will have them trained using content from the VR (virtual reality) safety training programs at our Plant Operation Technology Training Center, which is intended for them. This enables them to experience simulated hazards for the purpose of cultivating human resources who have high sensitivity to danger. Through these efforts, we will also enhance education in order to reduce occupational injuries among construction subcontractors.
*1 Serious Occupational Injuries:
Occupational injuries that fall under disability grades 1 to 7, causing death, injury or illness.
*2 Work-related Significant Occupational Injuries:
“Work-related Significant Occupational Injuries (WSOIs)” refer to occupational injuries that resulted in absence from work or death. WSOIs also include lighter occupational injuries that may lead to absence from work or death due to the potential danger in the cause of the injury. WSOIs do not include injuries that are not directly related to operations. In its definition of WSOIs, the Group not only includes occupational injuries that result in absence from work, but also lighter occupational injuries that may not result in absence from work but have serious causes of injuries. The Group monitors the WSOIs frequency as a KPI as well.
Please refer here for Lost-Time Injury Frequency Rate (LTIFR).
Comparison of Occupational Injury Frequency between Mitsui Chemicals, the All Industries in Japan and the Japanese Chemical Industry
*Occupational injury frequency = Number of individuals killed or injured by occupational accidents x 1 million hours / Total working hours for all employees.
The figures for the all industries in Japan and for the Japanese chemical industry indicate the Days Away From Work Case (DAFWC) frequency.
Sources:
*1 Ministry of Health, Labour and Welfare White Paper Survey on Industrial Accidents Occupational Injuries
*2 Japan Industrial Safety & Health Association “General Guidebook on Industrial Safety” Significant Occupational Injury Frequency
Work-related Significant Occupational Injuries Frequency
*Includes contractors operating on site.