The Mitsui Chemicals Group established its first Plant Operation Technology Training Center in Mobara in 2006, and then in Nagoya in 2007, to train plant operation personnel. Chemical plant operators are trained in Mobara, and the Nagoya center provides training programs for operators of fabricated products plant. We are striving to develop a pool of talent who are "strong in operations and facilities with a focus on safety" through hands-on, experiential training utilizing DX technology, including simulated experience training using virtual reality (VR) technology, targeting not only our Works but also our R&D centers and indirect departments, as well as employees of our domestic and overseas affiliates.
Safety and Prevention
Plant Operation Technology Training Center
Mitsui Chemicals’ Plant Operation Technology Training Center
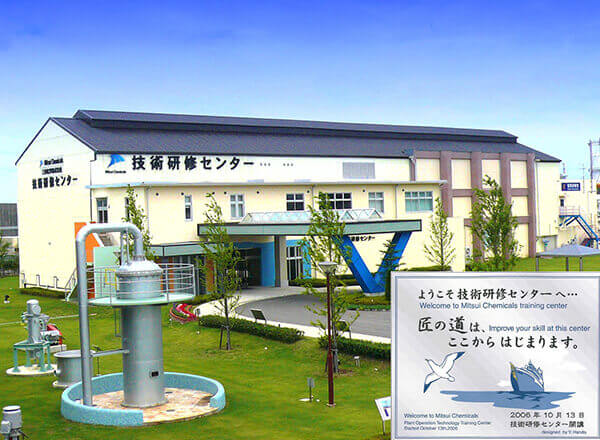
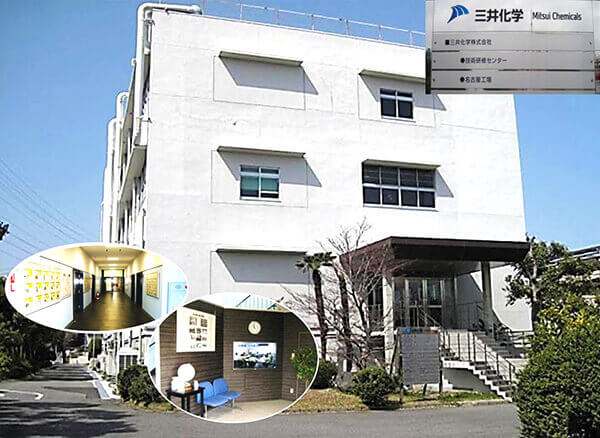
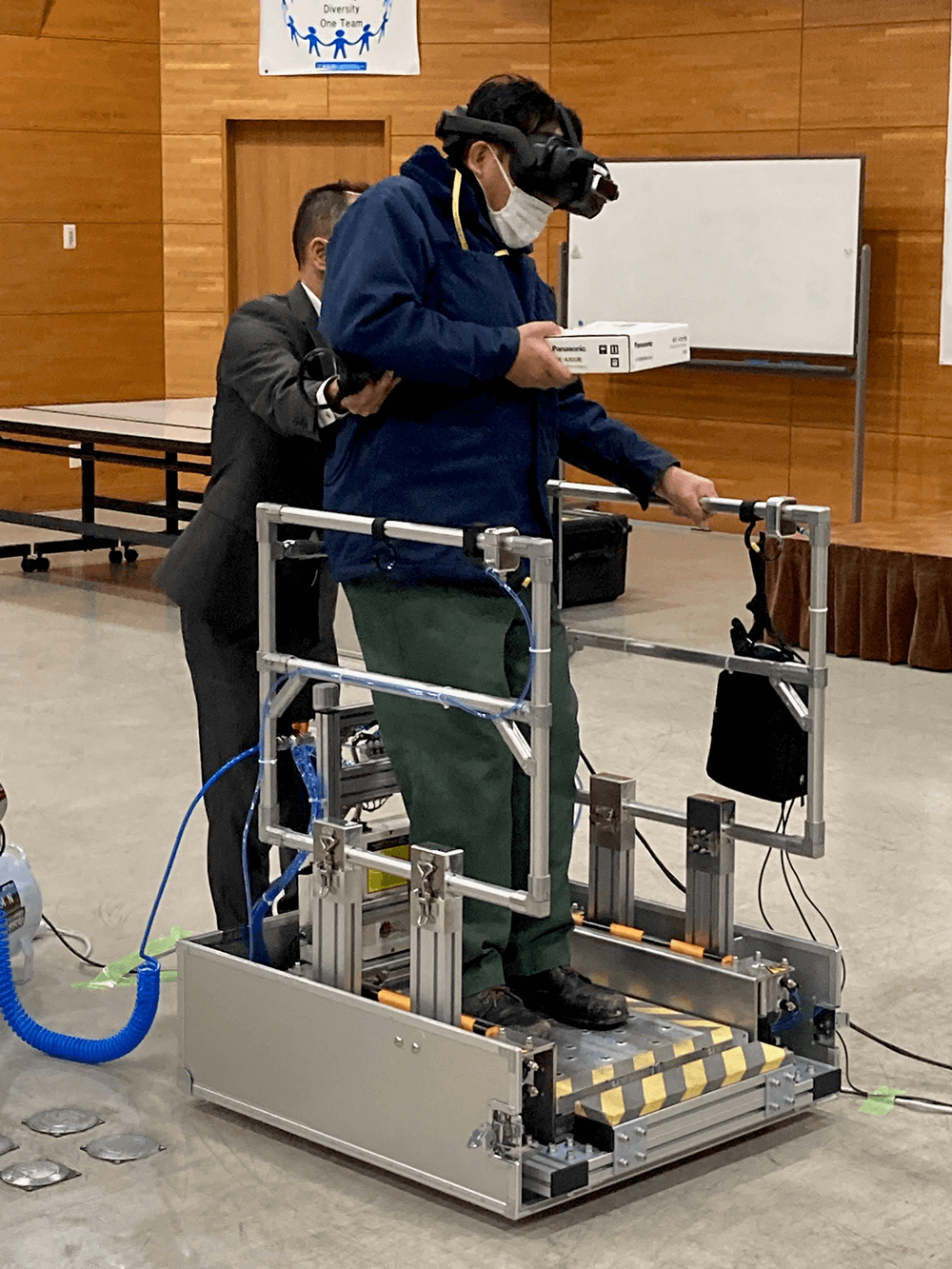
Mitsui Chemicals’ Plant Operation Technology Training Center (Mobara and Nagoya) Training Sessions for Mitsui Chemicals Group Employees
For Mitsui Chemicals employees | |||||
---|---|---|---|---|---|
Number of Attendees (Total Training Time) | |||||
FY2020 | FY2021 | FY2022 | FY2023 | ||
For Plant Operators | When joined Company | 5 (43hrs) | 16 (136hrs) | 8 (52hrs) | 17 (313 hrs) |
Follow-up training (six months after joining Company) | 90 (2,520 hrs) | 123 (3,443 hrs) | 147 (3,614 hrs) | 198 (2,938 hrs) | |
Promoted staff (3-4 years after joining Company) | 55 (1,540 hrs) | 77 (2,156 hrs) | 214 (2,804 hrs) | 97 (2,554 hrs) | |
Workplace managers (8 years or more after joining Company) | 18 (252 hrs) | 5 (70 hrs) | 23 (337 hrs) | 40 (587 hrs) | |
For Engineers | When joined Company* | 0 (0 hrs) | 32 (112 hrs) | 102 (510 hrs) | 116 (677 hrs) |
3-5 years after joining Company | 7 (147 hrs) | 23 (483 hrs) | 23 (449 hrs) | 41 (800 hrs) | |
For Researchers | 25 (263 hrs) | 81 (851 hrs) | 55 (413 hrs) | 91 (683 hrs) | |
Other | 119 (1,592 hrs) | 102 (459 hrs) | 67 (162 hrs) | 58 (567 hrs) | |
For employees of affiliates | |||||
Number of Attendees (Total Training Time) | |||||
FY2020 | FY2021 | FY2022 | FY2023 | ||
Domestic Subsidiaries & Affiliates | 199 (1,592 hrs) | 326 (2,608 hrs) | 291 (2,680 hrs) | 183 (1,686 hrs) | |
Overseas Subsidiaries & Affiliates | 0 (0 hrs) | 0 (0 hrs) | 21 (254 hrs) | 31 (1,819 hrs) | |
Total | |||||
Number of Attendees (Total Training Time) | |||||
FY2020 | FY2021 | FY2022 | FY2023 | ||
518 (6,893 hrs) | 785 (10,319 hrs) | 951 (11,275 hrs) | 872 (12,623 hrs) |
*Switched to web training in fiscal 2021
Web Training
The Plant Operation Technology Training Center was quick to start developing web training programs and provides simulated training programs as substitutes of physical training programs to the Company’s plants and the Group’s domestic and overseas affiliated companies.
The programs were all tailored to order. We designed the curriculums to meet the needs of individual companies by taking into account the skill level of trainees and the likely risks they may encounter. We also provide training in local languages, including English, Chinese, Malay, Indonesian, Spanish, and Dutch, using AI-based simultaneous translation. Attendees have reported that the web training programs are easy to understand and provide a good insight into the work, even though they cannot physically experience it. Although we recognize that such web training programs cannot replace real physical training programs, we continue utilizing it as a sustainable training style that is suitable for the digital society, with benefits such as not requiring lecturers and trainees to travel.
Web Training Overview
Concept | Hybrid (lectures, demonstration images, and pre-recorded videos) and interactive (questions and group discussions) simulations of physical training programs. | |
---|---|---|
Program contents | Programs made to date | In addition to contents on safe operations, such as pointing and calling, static electricity and dust explosions, oxygen deficiency and poisoning, burns and chemical injury, falling and dropping, and pinching and rolling, we also provide equipment-related contents, such as the basics and problems found in machines, instrumentation, and electricity. |
Future plans | All the experience-based programs currently available will be converted to web training, except those for plant operations and non-routine work. A virtual tour of the Training Center is planned. | |
Operation |
|
Domestic and Overseas Web Training
Number of Attendees (Total Training Time) | ||||
---|---|---|---|---|
FY2020 | FY2021 | FY2022 | FY2023 | |
Mitsui Chemicals, Inc. and Domestic Subsidiaries & Affiliates | 143 (40 hrs) | 748 (2,992 hrs) | 782 (3,552 hrs) | 604 (2,379 hrs) |
Overseas Subsidiaries & Affiliates | 10 (3 hrs) | 174 (696 hrs) | 211 (513 hrs) | 269 (661 hrs) |
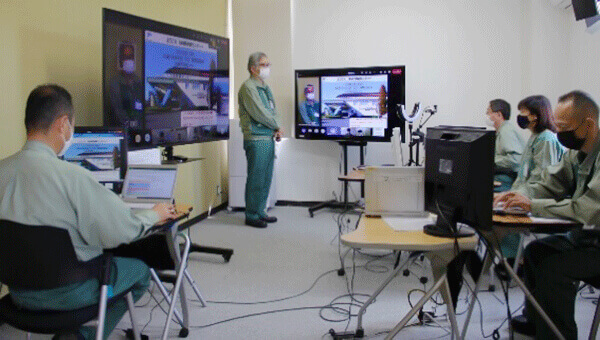
Web training: Questions from the trainer
Encourage attendees’ thinking and discovery
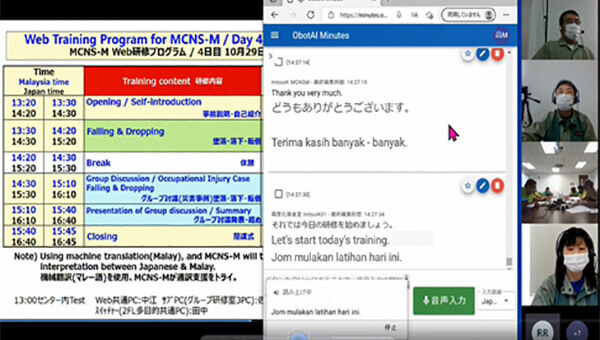
Screen showing training utilizing real-time AI-based translation
(Training textbook, translation software, and monitors showing participants)
On-site Training (VR Training)
Since the COVID-19 pandemic made it impossible for training center staff to visit Works to provide training, we improved the operation of VR training in fiscal 2020 and established a new training system that involved loaning equipment to the Company's Works and affiliates. In fiscal 2023, approx. 670 employees at our five Works and 509 employees of our affiliates took the course. The programs are particularly effective in preventing occupational injury and raising safety awareness among new employees. We will further expand the target audience with additional content for our contractors and R&D divisions in the future.
VR Safety Training
Objective | Enhance training curriculum and improve training effectiveness through the utilization of VR | |
---|---|---|
Expected Effects | (1) Increase sensitivity to danger by experiencing accidents in a virtual space that cannot be experienced under normal circumstances (2) Less restrictions on training location and time, and training can be conducted with a large number of participants | |
VR tools | Mobara Training Center | 3 sets |
Nagoya Training Center | 1 set | |
Program contents | Forward-facing crash/fall, conveyor belt pinch, fall while descending stairs, roller entrapment, crash and fall (customized version), vent clogging, blowout ignition, dust explosion, residual pressure blowout during piping maintenance, power panel electric shock, forward/backward movement of forklifts, disk grinder kickback, cutter operation, reaction explosion in a flask, glass tube assembly cut, etc., are provided. |
On-site Training (VR Training)
For Our Group employees | ||||
---|---|---|---|---|
Number of Attendees (Total Training Time) | ||||
FY2020 | FY2021 | FY2022 | FY2023 | |
On-site Training (VR Training) | 283 (2,264 hrs) | 1,287 (5,148 hrs) | 1,093 (4,682 hrs) | 1,178 (4,712 hrs) |
Globalization of Training Centers
Since fiscal 2018, we have been proactively focusing on developing human resources that will serve as the foundation to support the global business of the Group. We offer educational programs and training support not only for Mitsui Chemicals but also for domestic and overseas subsidiaries and affiliates, customizing them to the specific needs of each company.
For affiliates in the Southeast Asia region, the Operation Excellence Training Center (OETC) of the Siam Group in Thailand has been giving training courses in Thai and English. The Siam Group is capable of providing the same level of training as in Japan, utilizing the training system and knowhow licensed from us. In addition, with training in local languages now feasible using AI-powered simultaneous interpretation, online training has helped to increase training opportunities for overseas affiliates, such as organizing curricula in accordance with the needs of each company.
Training Centers Available to Other Companies
Our training centers have been open to other companies since fiscal 2015 so that they can train their employees to handle hazardous materials. The demand for human resource development and training for production site safety is extremely high, and many companies from different industries utilize our Centers. Our programs are highly rated by attendees with comments such as: “I learned many things that I can utilize in my company,” and “It was easy to understand through experienced-based training through case studies of past accidents and injuries.” In fiscal 2023, the number of participants for training courses and visitors from outside the company increased significantly as COVID-19 was downgraded to Category 5 and the pandemic, which had lasted for more than three years, finally came to an end.
External Training Sessions (Mobara) / Responses to Center Tour Requests (Mobara and Nagoya)
FY2020 | FY2021 | FY2022 | FY2023 | |
---|---|---|---|---|
Number of Training Attendees | 109 | 106 | 221 | 265 |
Number of Center Visitors | 35 | 51 | 99 | 230 |
We open our training centers as training sites for outside companies, aiming to help build a society with zero industrial accidents and injuries.
We are also in charge of creating training contents for Keiyo Human Resource Development Association, which was jointly established by Keiyo Industrial Complex companies.